
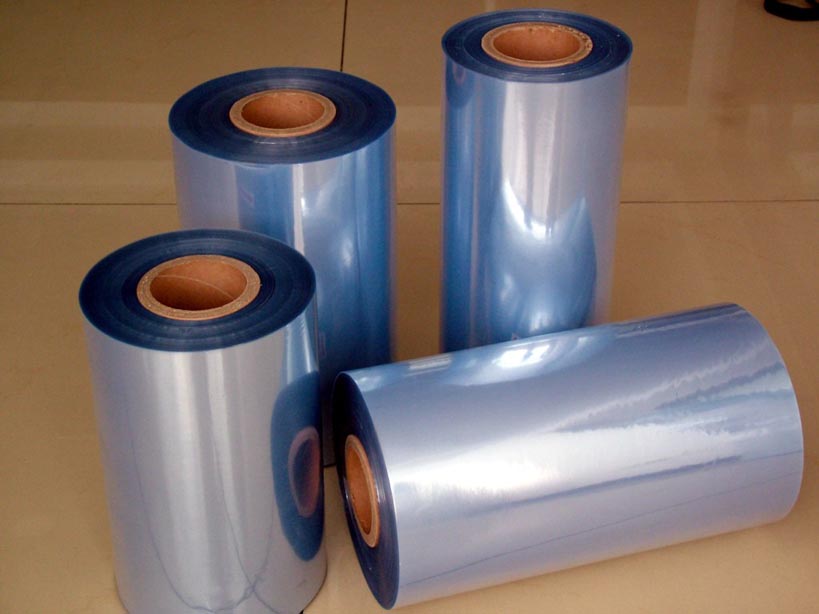
Small holes may be poked in the film before wrapping to allow air to escape while the film is shrinking. Goods are packaged by wrapping the film loosely around the goods, sealing the film to make a completely enclosed bag, and then shrinking the film in a shrink tunnel or oven. It is distinguished from regular shrink film by its superior clarity and appearance as well as increased shrinkage properties and higher stiffness. Oriented, high-clarity shrink film is used to protect and display high-value consumer goods. Spherilene Process High Performance LLDPEs 2 are shown to be a viable solution. 1 The cost of mPEs, however, still tends to be very high, lessening their impact on the conventional blown film shrink market. Metallocene polyethylenes, mPEs, have been likewise explored as an alternative to LDPE in this market and have been found to shrink in the TD. This expansion leads to loose packages that do not effectively unitize goods. Conventional LLDPE resins will yield film strength enhancements as well as an ability to downgauge, but films made from these resins will, instead of shrinking in the transverse direction, TD, expand upon heating. Shrink film manufacturers are currently looking for resins that will allow the production of a higher performance film (bringing value to their customers) or downgauging (bringing cost savings).
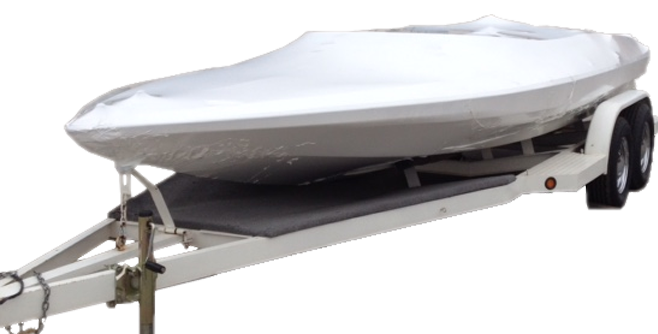
LDPE-rich blends with LLDPE, high density polyethylene, and ethylene vinyl acetate copolymers are used to overcome some of these deficiencies, as needed, in various premium, freezer, and high tensile film applications. However, they don't downgauge well, have a tendency to form holes easily during the shrinking process, have relatively low physical properties (tensile strength, puncture, and tear resistance), and are generally more expensive than linear low density polyethylene, LLDPE.

The most typical LDPEs used in this application are autoclave resins with melt indices around 0.4-0.7 g/10 min and tubular resins with melt indices around 0.2-0.3 g/10 min.įilms made from these LDPEs have very good shrink performance, give tight packages when unitizing goods, and heat seal at low temperatures. The conventional blown shrink film market is dominated by high pressure low density polyethylene, LDPE. Two general categories of shrink film exist-specialty shrink film produced via some extra-orientation process (such as tentering or double-bubble blown film fabrication) and industrial shrink film produced via conventional blown film fabrication. Once wrapped, the package is exposed to a thermal treatment (such as via a forced convection oven or heat gun) to tighten the film. Shrink film is used to bundle, collate, or over-wrap products for unitization, display esthetics, and/or tamper resistance. Cowell, in Metallocene Catalyzed Polymers, 1998 INTRODUCTION
